Kaolin and Kaolin Dryer
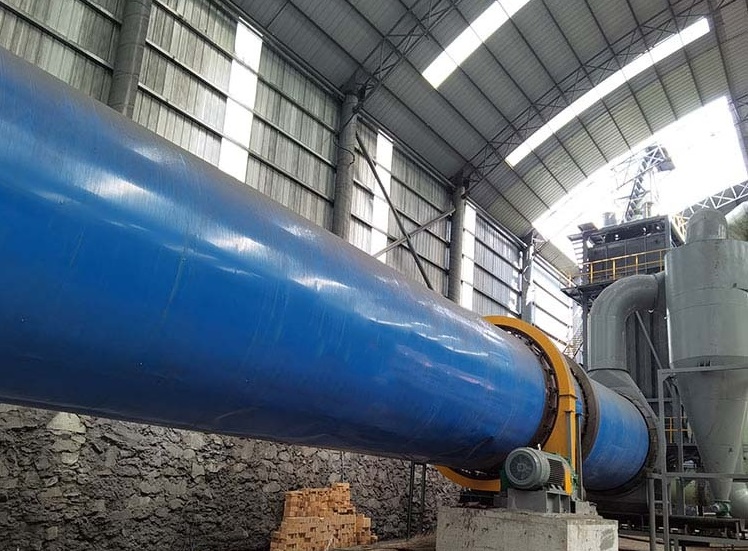
Kaolin is a non-metallic mineral, a kind of clay and clay rock mainly composed of kaolinite clay minerals. Kaolin contains elements such as aluminum, silicon, and oxygen, and has low crystalline moisture. Pure kaolin is white, delicate, soft and earthy, and has good physical and chemical properties such as plasticity and fire resistance. Due to its excellent physical and chemical properties, kaolin is mainly used in ceramics, enamel, porcelain, ceramic tiles, refractory materials and other industries; secondly, it is used in coatings, rubber fillers, enamel glazes and white cement raw materials; in small quantities, it is used in plastics, paints, Pigments, grinding wheels, pencils, daily cosmetics, soaps, pesticides, medicines, textiles, petroleum, chemicals, building materials, national defense and other industrial sectors.
Based on the research on kaolin, we have specially developed a professional dryer for kaolin (It is mainly used for drying kaolin and other types of soil and mud) and we already solve the problems of material sticking to the wall, crushing and drying.
Kaolin Dryer Heat Source
Kaolin Dryer can adapt to a variety of fuels such as coal, oil, and gas. At present, boiling furnaces are favored by users because of their easy operation, energy saving, environmental protection, and easy purchase of raw materials. Some manufacturers also use natural gas or use a gas generator for conversion, and the gas undergoes secondary combustion to achieve the drying effect.
Working Principle of Kaolin Dryer
The kaolin drying system mainly consists of a hot air furnace, a belt feeding conveyor, a drum dryer, a belt discharge conveyor, an induced draft fan, a cyclone dust collector, a dust collector and an electrical control system. The equipment adopts downstream drying process.
The working principle of the kaolin dryer is as follows: after the wet material enters the drying drum, it is divided into the following working areas: First, the guide area. The mineral slag enters this area and contacts the high-temperature hot air to quickly evaporate the water. The material is guided at a large guide angle. When the plate is moved, it is introduced into the next work area; the second is the plate copying area, where the mineral slag is lifted up by the plate to form a material curtain state. At this time, the material is in full contact with the hot air, and the water in the mineral slag evaporates quickly. Stripped into water vapor, the water vapor is immediately pumped away by the induced draft fan to achieve the purpose of drying the mineral slag; the mineral slag is dried in this area into a loose state with a moisture content of less than 5% (or lower). After heat exchange When the material reaches the required moisture state, it enters the final discharging area; the third is the discharging area. The drum does not have a lifting plate in this area, and the material rolls and slides to the discharge port in this area to complete the entire drying process.