Only 5% of lithium-ion batteries collected are recycled, wasting valuable materials that could make electric vehicles more sustainable and affordable.
There is strong potential for the battery recycling market to grow and supply a large portion of current market needs.
The private sector must jumpstart battery recycling at scale by investing in innovation.
According to a 2019 report by the US Department of Energy (DoE), only 5% of lithium-ion batteries are collected and recycled. While that same report estimates that recycled material has the potential to meet one-third of the US’ cathode material needs by 2030, more needs to be done to move the industry to where it needs to be.
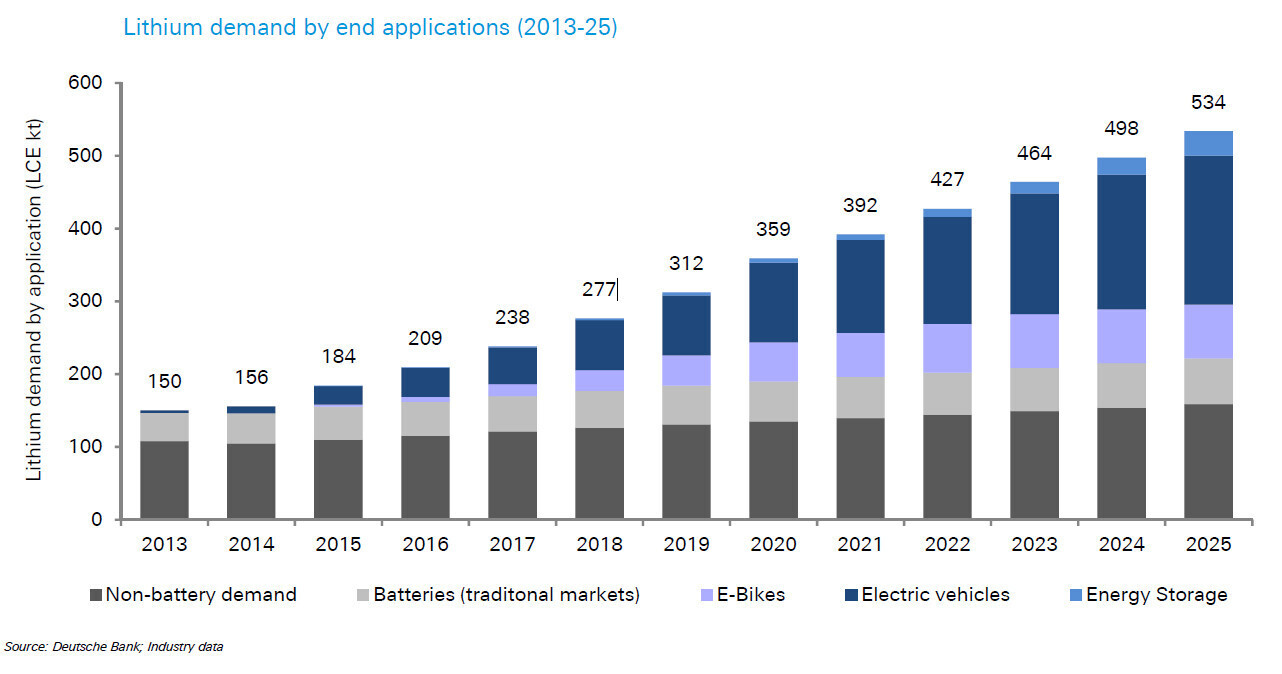
On the regulatory front, the work has just begun. This past winter, the state of New Jersey made it illegal to discard electric vehicle (EV) batteries in landfills. Conversely in Europe, a recent law will require new batteries to contain at least 6% recycled lithium and nickel by 2031. While action from governments is encouraging, its success depends on industry-wide support.
The future of lithium-ion battery recycling
The question that we should be asking is what the future of battery recycling could look like. Will we be reusing valuable materials to close production loops? Or will disparate policies make battery recycling next to impossible and financially prohibitive? Far from being a “wait and see” that requires public sector mandates, the private sector now has an opportunity to show up as responsible players in driving sustainable production practices and do what it does best: innovate in material development and scale technologies.
Already, we have seen encouraging momentum. The ICCT estimates that US lithium-ion battery recycling facilities can currently process about 100,000 tons each year and planned projects over the next decade are expected to scale up capacity to more than 650,000 tons.
With the first wave of EVs now nearing end of life, now is the time for the private sector to double down on battery investment. It’s up to us to drive the “sustainable” EV transition and the future we want to see.
The value of recycling
Being able to power up your car to drive hundreds of miles on clean energy is an engineering feat as well as major step in decarbonization. However, the materials used inside EV battery casings are both costly and finite. Metals used in the battery cathode such as cobalt, nickel, manganese and lithium can cost anywhere from $4 to $35 per kilogram. Without metal recovery, we could experience a supply deficit by the 2030s. While the barriers to recycling earth metals have historically included everything from inconsistent battery collection practices to concerns about explosion risks at recycling facilities to prohibitive processing costs, the reality is that advances in process and material innovation are steadily driving down recycling costs just as lithium chemistries are being improved.
The value of recycling batteries extends beyond the cost of materials. For many countries, it’s also a matter of national security. China controls 90% of the EV battery material supply chain, so shoring up recycled materials and local supply chains can help entire countries withstand volatility.
As we think about the value of recycling batteries, we should consider the costs of not doing so. Throwing away batteries wastes precious resources and expands the large carbon footprint created by continually processing virgin materials. In addition, there are both human and environmental costs to not recycling. For example, processing virgin ore to useful metals has an impact on water use, energy use and could impact the environment negatively. The overall virgin process has a higher carbon footprint than using recycled materials. In fact, when environmental and energy costs are taken into consideration, the cost of recycling is 10 times cheaper than manufacturing.
Innovations on the horizon
On the innovation front, three main areas in battery recycling show strong economic potential as well as the promise of positive impact.
The first is graphite recycling, which has emerged as a key area for step improvements. There are indications that battery performance can be further improved through adding fluorine into graphite recycling to slow down chemical reactions and degradation within the battery. The second is electrolyte recovery, which can be challenging due to its chemical instability and complex removal process. However, researchers are attempting to find a way to do this more efficiently. The third is lithium extraction, which new techniques and technology are in development that can extract LiPF6 and lithium salts from black mass.
While these process technologies are nascent, companies are proving that it can be done. For example, Orbia recently announced a partnership with Ascend Elements to scale up a process technology that can be used to yield 99.9% pure graphite from spent batteries. In addition, Orbia is working on a US Department of Energy-supported project with the National Renewable Energy Laboratory to create a room temperature graphite recycling process as well as with the Idaho National Laboratory to find ways to recycle electrolytes and reuse electrodes. Pioneering players such as Nth Cycle and Redwood Materials are also exploring electro-extraction technology as an alternative to hydrometallurgy and closed-loop extraction processing respectively.
Lithium-ion battery recycling is an important problem we must solve through innovation to provide sustainable solutions for battery material needs. It is possible to recycle; we only have to look to the success of lead acid batteries that are largely recycled today. The imperative to invest in our lithium-ion battery recycling process is clear. Now we must do the hard work to continue innovating and move ahead at full charge.